Wholesaler case
Typical Case of Wholesaler:
This customer made a blanket order at one time in which an average number of 10 high cube containers were required to be shipped at once. Such a order made it very difficult to manage and operate the overall supply chain: ① customer demand points were dispersive, numerous technical standards were required;
② product categories were many and complex, some products required of new development; ③ there were large differences in the number of products; ④ there were numerous suppliers, which were difficult to be planed as a whole and coordinated; ⑤it was complex to control quality and delivery; ⑥ cargo stowage was complex, missing of any single document could affect the entire ticket declaration.
To ensure that orders could meet customer demand and the goods could be safely shipped on schedule with quality and quantity guarantee, we set up a special order-based project team (together with customer and suppliers), to carry out overall planning, monitoring and control for the order according to scientific project management methods. The team gave full play to the spirit of collaboration, and team members analyzed order-related difficulties together, and timely solved any problem emerging in the whole process. Finally, the goods successfully passed SGS testing, and were successfully delivered to the customer. The customer was highly satisfied with our systematic operations, and made zero complaint to the product quality.
Typical Case of Wholesaler:
This customer made a blanket order at one time in which an average number of 10 high cube containers were required to be shipped at once. Such a order made it very difficult to manage and operate the overall supply chain: ① customer demand points were dispersive, numerous technical standards were required;
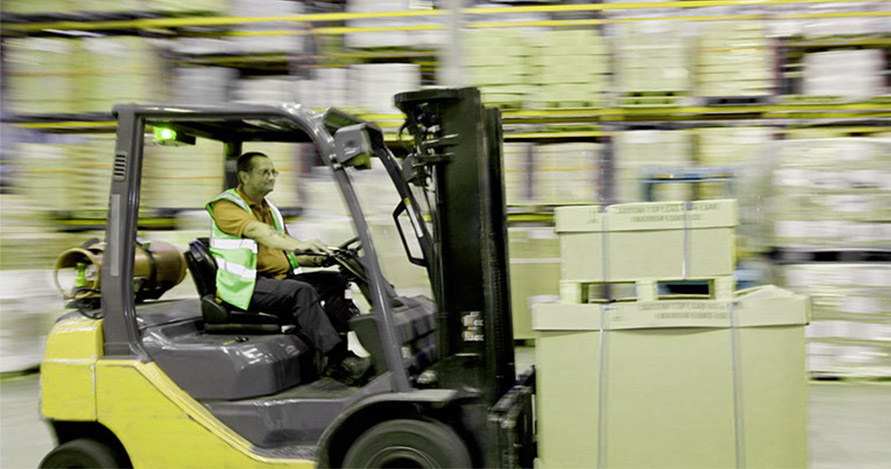
Retailer case
Typical Case of Supermarket Customer:
This customer made a blanket order at once, requiring partial shipments, with an average two containers per month. This customer had extensive distribution channels, thus the goods needed to be shipped to different areas. Such order made it very difficult to manage and operate the overall supply chain: ① supermarket customer’s product categories were complex, and small in quantities; ② delivery requirements were very strict, and continuous goods supply must be ensured; ③ Requirements for product packaging details were demanding; ④ product quality must be high, and service must be responsive; ⑤ there were numerous suppliers, which were difficult to be planned as a whole and coordinated; ⑥goods must be shipped for many times, which required of repeating order operation processes. To ensure that the order could meet the customer demand; good-selling goods could be supplied continuously;
and backlog of unsalable goods could be avoided, we set up a special order-based project team (together with customer and suppliers), to carry out overall planning, monitoring and control for the order according to scientific project management methods. When the order initiated, we made use of our familiarity with regional markets and industries, and our grasp of market trends, to actively recommend good-for-sales product categories to the customer. Besides, together with this supermarket customer, we studied and customized a unique packaging attractive to customers, and we made sure that goods could be shipped within the delivery date. We gave full play to the spirit of collaboration, to carry out systematic control of supplies in an overall manner, including co-developing feasible production plans, co-coordinating and co-auditing raw material supplies (the suppliers of suppliers), timely analyzing and processing order changes, and strictly controlling the delivery cycle. Finally, the goods successfully passed SGS testing, and were successfully delivered to the customer. This customer showed greatest satisfaction with our overall planning and operations, and the cooperation of both sides thus deepened continuously.
Typical Case of Supermarket Customer:
This customer made a blanket order at once, requiring partial shipments, with an average two containers per month. This customer had extensive distribution channels, thus the goods needed to be shipped to different areas. Such order made it very difficult to manage and operate the overall supply chain: ① supermarket customer’s product categories were complex, and small in quantities; ② delivery requirements were very strict, and continuous goods supply must be ensured; ③ Requirements for product packaging details were demanding; ④ product quality must be high, and service must be responsive; ⑤ there were numerous suppliers, which were difficult to be planned as a whole and coordinated; ⑥goods must be shipped for many times, which required of repeating order operation processes. To ensure that the order could meet the customer demand; good-selling goods could be supplied continuously;
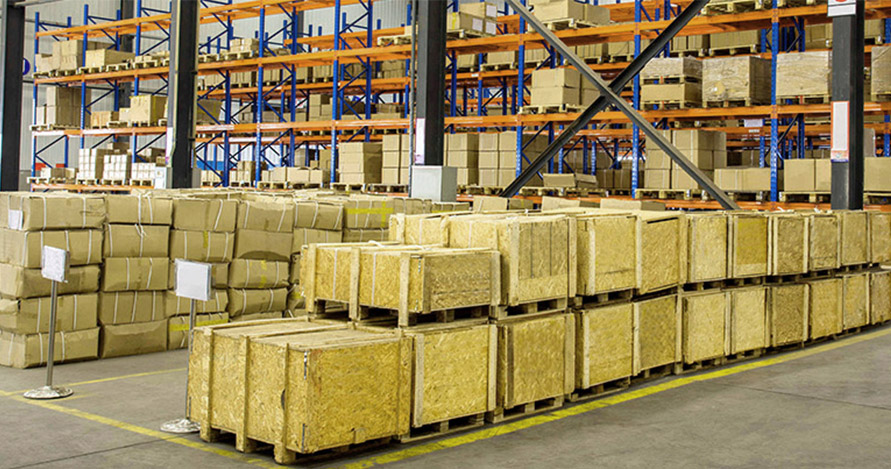